SMT Mounting Machine Classification
Jul 01, 2020 Editor: admin
Preface
The basic principles of all placement machines are the same, and the placement of components is realized through the basic steps of circuit board entry, positioning, component absorption, identification and placement. With the development of placement technology, various placement machine developers and manufacturers have developed a variety of placement machines to meet the needs of the market. In addition to the three different development stages of the placement machine mentioned above, according to different markets, different characteristics of various products, different requirements of production characteristics, and different design concepts of equipment manufacturers, placement machines can be divided into different categories in terms of speed and function.I,Classification by speed.
The placement machine is generally divided according to the speed, there is no specific limit, according to the custom, according to the mounting speed of the components can usually be divided into the following categories.
(1) medium and low speed placement machine.
The theoretical mounting speed of the medium and low speed placement machine is less than 30000 pieces / h (chip components).
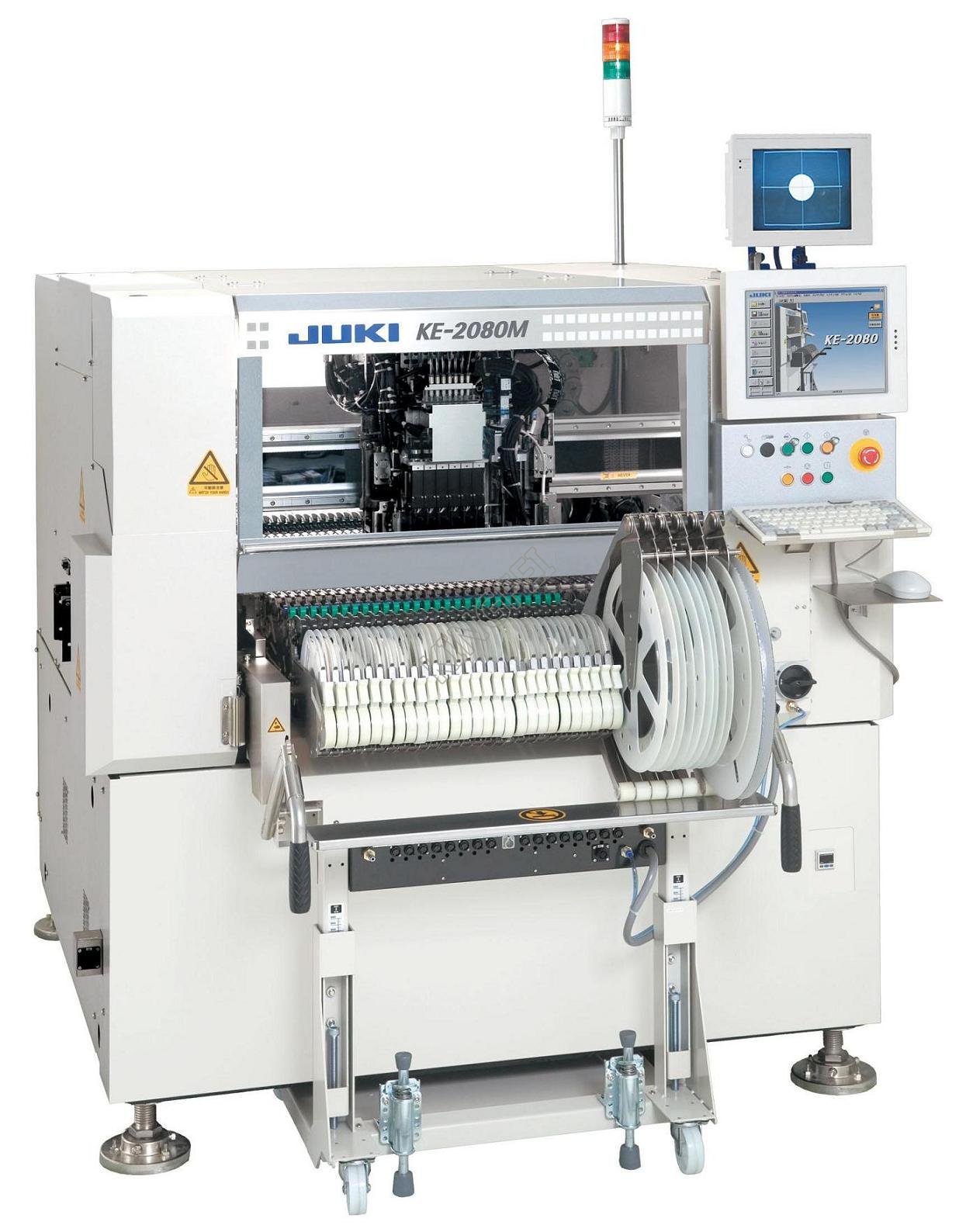
In the early days of the development of surface mount technology, placement machines with a chip speed of more than 14000 pieces / h can be called high-speed placement machines, such as CP2 and TCMV800 machines. With the development of surface mount technology and automation technology, the speed and accuracy of placement machine are getting higher and higher, and the division standard of high-speed placement machine is also improved. Now it is widely believed that the theoretical speed of the medium-speed placement machine, for example, the AdVantis AC-30L, of Global Instruments has reached 30000 chips / h.
Some placement machines are mainly used for mounting large components, high-precision components and special-shaped components, as well as small sheet components. This kind of placement machine is functionally a multi-function placement machine (Multi-Function Placement Machine),), but because their theoretical speed is between 3000,20000 chips / h, they are also classified as medium speed placement machines if they are classified according to speed.
(2) High speed placement machine.
The theoretical mounting speed of the high-speed placement machine is 30000 to 60000 pieces / h.
High-speed placement machine is mainly used to mount small chip components and small integrated components, and some high-speed machines also have the function of small mounting spherical matrix element (BGA). The turret structure is commonly used in the high-speed placement machine, and the compound structure is also adopted more often. The high-speed machine mainly considers the mounting speed and stability in the design, and realizes the high-speed mounting under the precision of micro-chip assembly. High-speed placement machine is widely used in large electronic manufacturing enterprises and some professional original equipment manufacturing enterprises (OEM).
Like the medium-speed placement machine, with the development of science and technology, the speed of the high-speed placement machine is getting faster and faster, and the speed of the high-speed placement machine is also increased from 14000 pieces / h to nearly 60000 pieces / h. The design of the placement machine has also developed from the main consideration of speed to the consideration of high mounting precision, high reliability, multi-function, easy operation and maintenance and the ability to quickly change products.
(3) Ultra-high speed placement machine.
The theoretical mounting speed of the ultra-high speed placement machine is higher than 60000 pieces / h.
Ultra-high-speed placement machine is also a higher-speed placement machine developed on the basis of high-speed placement machine. In addition to mounting small chip components and small integrated components, some of these placement machines can also mount spherical matrix elements (BGA). In addition, some ultra-high-speed placement machines are equipped with high-precision multi-function placement head, which has become a high-speed multi-function placement machine which can mount not only small components but also large-scale, high-precision and special-shaped components.
The structure of ultra-high-speed placement machine generally has two kinds of structure: compound structure and large-scale parallel structure. In the earlier period, the representatives of ultra-high-speed machines are Assembleon FCM with large parallel structure and Siemens HS50 with dual working platform. In recent years, various major suppliers of placement machines have launched their own ultra-high-speed placement machines, such as global Genesis and other companies' products. The mounting speed of large parallel ultra-high-speed placement machine is related to the number of modules. For example, a large parallel ultra-high-speed placement machine can be configured with 20 modules, and the theoretical mounting speed can reach up to 150000 pieces / h. The theoretical mounting speed of the latest composite ultra-high-speed placement machine can also reach 120000 pieces / h, such as Global Genesis GC-120Q
II. Classification by function.
There are a variety of components that can be assembled by machines on the circuit boards of some complex electronic products, including common chip components, a variety of chip integrated circuits ((IC),), spherical matrix elements ((BGA)), connector socket (Connector), electrolytic capacitor (ALC), indicator lights and other special-shaped components. Components are also packaged in a variety of ways, such as Tape& Reel, tube (Tube), disk (Tray), boxed (Bulk) and so on. On the other hand, the mounting range of a single mounting head of the placement machine is limited, and generally can not cover all the component range (as shown in figure 2.1) and packaging, so it is impossible to mount small sheet components at a high speed on a machine or a functional module. it can also accurately mount special-shaped and high-precision components. Therefore, most of the placement machines can be divided into the following categories according to different functions.
1. High-speed placement machine.
The early high-speed placement machine especially refers to the shooting machine specially used for chip component placement. With the development of technology, the concept of high-speed machine is also changing. As mentioned earlier, in terms of speed, the placement machine can be divided into medium-speed placement machine, high-speed placement machine and ultra-high-speed placement machine; functionally, the placement machine specializing in high-speed placement of small and medium-sized components is also called high-speed machine. Some medium-speed placement machines and ultra-high-speed placement machines specializing in high-speed placement of small and medium-sized components also belong to high-speed machines in function.
The high-speed placement machine has the following characteristics:
The high-speed machine can adopt various structures. In small and medium-sized production enterprises and scientific research and experimental units, platform medium-speed placement machines are widely used as high-speed machines. Turret structure placement machine used to be the main force of high-speed machine in large-scale production, but now composite structure and large-scale parallel structure placement machine has a great tendency to replace turret placement machine.
(2) the mounting range of the components of the high-speed machine is generally narrow, and the components that can be mounted generally range from 01005 (0.4mm×0.2 mm) to 24mm × 24mm, and the height of the components is generally 6.5mm at most. Some of the maximum components of the high-speed mounting head can only reach 5mm × 5mm, and the height can only reach 3mm. The larger components need to be replaced with a wider range of mounting heads, or some nozzles are skipped when absorbing the components, but the mounting speed will be reduced as a result.
The packaging of 3 components can only be packed in tape and bulk boxes, and a small number of high-speed mounters can accept tube and plate materials, but some sacrifices will be made in speed.
4 most of the high-speed mounting heads can be mounted at full speed when absorbing and mounting small components (less than 4mm × 4mm). When absorbing and mounting larger components, due to the excessive speed of rotation, the rigid contact of the suction nozzle, the complexity of camera identification and insufficient vacuum suction and other reasons, the need to slow down in the component absorption, identification, correction and mounting links, thus affecting the production capacity of the whole machine.
(5) the suction nozzle of the high-speed placement machine is generally only vacuum nozzle.
(6) most of the high-speed placement machines realize high-speed placement at the expense of certain mounting accuracy and functions. Now the new type of compound and parallel high-speed placement machine can take into account the speed and accuracy of placement.
(7) most of the high-speed mounting heads have some limitations in component recognition, such as using recognition shape to correct most components, BGA ball detection is not a standard configuration, can not carry out "global testing" and so on.
Global Instruments has developed a high-speed placement head called "Lightning", which can be installed on different arched platforms of AdVantis and Genesis to become a high-speed placement machine. The mounting range of the mounting head is from 01005 (0.4mm×0.2 mm) to 30mm × 30mm, and the height is 6mm, and the material can be drawn from the disk feeder. The mounting head has two mobile cameras with an accuracy of 2.9 MPP and 0.9 MPP respectively, and has all the functions of identifying components such as BGA,Pattern and C4. Since each suction nozzle has an independent vacuum system and sufficient suction grip elements, when mounting larger components, there is no need to slow down and skip the suction nozzle, and all components with length, width and height below 6mm can be mounted at full speed.
2. Multi-function placement machine.
Multi-function placement machine (Multi-Function), also known as universal machine or high-precision placement machine, can mount high-precision large, special-shaped components, and generally can mount small chip components, which can cover almost all the range of components, so it is called multi-function placement machine. Because of the small packaging pitch of large devices, it requires high precision of the placement machine, so it is also known as high-precision machine.
The features of the multi-function placement machine are as follows:
The main results are as follows: (1) the structure of the multi-function placement machine mostly adopts the arch structure, which has the characteristics of high precision and good flexibility.
(2) the full closed-loop servo motor is mostly used in X and Y positioning system, and the linear raster encoder is used for direct position feedback to avoid the error caused by screw distortion. In some cases, double motors and double screws are used to drive on both sides of the platform in the Y axis, and the bilinear grating ruler is used for feedback, which can effectively reduce the waiting caused by the stillness of the mounting head and reduce the error caused by the non-synchronous deformation of the crossbeam. There are more advanced linear maglev motors, which not only have the technical characteristics of double-drive, but also have the characteristics of direct drive, less wear and tear of mechanical structure, fast feedback, quiet, easy maintenance and high precision.
(3) the multi-kinetic energy placement machine mostly adopts the circuit board fixed type, and uses the movement of the mounting head to realize the X and Y positioning, and will not cause the large or heavy components to shift because of inertia because of the movement of the table.
4 can accept all kinds of material packaging, such as reel packing, tube packing, boxing and disk packing. In addition, when the plate is loaded with more materials, a multi-layer special pallet feeder can be installed.
5 in addition to the traditional vacuum suction nozzle, special suction nozzles can be used for special-shaped components which are difficult to absorb. In addition, pneumatic grippers can be used for components that cannot be absorbed by vacuum nozzles (as shown in the following figure).
6 elements in the correction generally use up camera, with front light, side light, backlight and on-line light and other functions, can identify a variety of different components. If the size of the element is too large, a video (FOV), up camera that exceeds the camera can also be analyzed and corrected by multiple video photography. Some multi-functional placement machines are also equipped with a mobile camera on the mounting head, which can identify a variety of smaller components.
7 in some products, some punched plug-in (Pin in Paste) components also need to be mounted at the same time as other patch components and solidified by reflow solder. the insertion of this kind of perforated plug-in components requires the machine to have the ability to mount under high pressure. The mounting head of part of the multi-function placement machine has the ability of high pressure placement, and the mounting pressure can be controlled by the program, up to a maximum of 5 kg.
8 some multi-function placement machines can be equipped with flux dipping system (Flux Dipping Assembly), which can be used for component stack packaging (Package on Package) and flip chip (Flip Chip) placement.
9 some multi-functional placement machine can also be equipped with a glue head for dispensing before mounting, some components are filled with tin or the bottom is filled with (Under fill).
With the above characteristics, multi-function placement machine can deal with a variety of complex components, and is an indispensable equipment in the production of complex electronic products. In some scientific research, testing, trial production units, in the case of being able to accommodate the types of materials, only one or more multi-function placement machines are used for small batch production. However, the speed of multi-function placement machine in dealing with small chip components can not be compared with that of high-speed placement machine, and the mounting speed of some high-speed placement machines can reach 5 times and 10 times that of multi-function machines when mounting small chip components. Therefore, in medium and large-scale production, reasonable configuration is generally made according to the characteristics of the product, so that the efficiency of each equipment is close to the highest.
3. High-speed multi-function placement machine.
The general placement machine function is relatively simple, for complex products, we must use different functions of the placement machine for combined wiring to complete the placement of the whole product. At present, some compound placement machines and parallel placement machines install multi-function mounting heads or multi-function modules, so that not only small sheet components can be mounted at high speed at the same time, but also high-precision, large and special-shaped components can be mounted at the same time; almost all component packaging methods can be accepted, including disk-mounted component feeders.
1 some composite placement machines with double mounting platforms can be equipped with two crossbeams and two high-speed mounting heads on the first mounting platform of the machine, and one or two crossbeams on the second mounting platform. a high-speed placement head and a multi-function placement head, and can be equipped with multi-disk disk feeder. In this way, this placement machine can mount not only small and medium-sized components at high speed, but also large and special-shaped components, thus becoming a high-speed multi-functional integrated placement machine.
The typical composite placement machines with this structure are Panasonic CM602C, Siemens HF3 or D3 platform, and Global Quadris or Hitachi GXH platform (as shown in the following figure).
(2) in the rear module of the parallel structure ultra-high-speed machine, the mounting head can use either a general high-speed mounting head or a high-precision mounting head with a suction nozzle. High-precision mounting head can mount a variety of high-precision, special-shaped components, can use a variety of special suction nozzles and mechanical claws. In this module, various feeders can be configured, including multi-disc feeder and so on. Together with the front high-speed module, this multi-function module forms a high-speed multi-function production line (as shown in the following figure).
III. Other ways of classification.
In the classification of placement machine, there are some other classification methods, such as classification according to the structural characteristics of the machine and according to the degree of automation of the placement machine process, and so on. In addition, in electronic assembly, there are some machines that work in a way similar to the placement machine, and some can even be cross-used in function, such as semiconductor mounting equipment and multi-function assembly unit.
1. Classified according to the degree of automation.
According to the degree of automation, the placement machine can also be divided into three types: fully automatic placement machine, semi-automatic placement machine and manual placement machine.
(1) automatic placement machine at present, most of the placement machines are fully automatic mechatronics placement machines, such as those with various speeds and functions described above, are fully automatic placement machines.
(2) the semi-automatic placement machine adopts manual upper and lower circuit board and manual patch position adjustment, and the action of suction and mounting can be completed automatically. This kind of placement machine can only mount a few components at the same time, if there are more components need to be adjusted (as shown in the following figure). This kind of placement machine is only suitable for some R & D institutions to use as a model.
(3) Manual placement machine.
This kind of placement machine requires the operator to move the patch head to the top of the component, and the component will be automatically sucked up by the vacuum suction nozzle, and then move the patch head to the corresponding bonding pad of the circuit board, rotate the patch head, and simply press the patch head downward in a good position. at the same time step on the pedal switch, vacuum off, complete the assembly of this component (as shown in the following figure).
2. Flip chip mounting equipment.
Flip Chip (Flip Chip,FC) placement belongs to advanced semiconductor assembly (Advanced SemiconductorAssembly) technology. Common applications include wireless antennas, Bluetooth, hard disk heads, component packaging, smart sensors and some medical high-precision equipment. Due to the small size of FC and small pin spacing, the same process can not be used with general surface mount components. The special semiconductor component placement equipment is similar to the high precision surface mount equipment, in addition to higher precision, it also needs some special unit modules for semiconductor placement. Common semiconductor placement devices include Datacon's Quantum 8800 and APM 200, Global GSM xs and AdVantis xs and so on. The following is an example of Global GSM xs ((shown below) to briefly introduce the characteristics of semiconductor mount equipment.
The basic structure of the machine is the same as that of many multi-function placement machines, and the arch structure is generally adopted. As there are not many kinds of components, they are generally smaller. The X and Y positioning system adopts full closed-loop feedback of linear motor grating ruler, and the mounting accuracy can reach more than 10 μ m @ 3 σ.
(2) the structure of the transmission board mechanism is the same as that of the multi-function placement machine, which adopts the way that the circuit board is fixed on the worktable. As most of the substrates mounted on flip wafers are on soft circuit boards, ultra-thin circuit boards and some special vehicles, flip wafer mounting equipment provides high-precision circuit board support lifting platform with vacuum adsorption function (as shown in the following figure).
(3) the mounting head with single suction nozzle or parallel suction nozzle is adopted, the mounting pressure can be controlled from 20 g to 2500 g, and the mounting nozzle is roughly the same as the general suction nozzle.
4 element recognition can be configured with a maximum resolution of 0.2 ft (1ft=30.48 cm) per pixel top camera can recognize a ball with a minimum 0.05mm. Circuit board recognition Downview camera uses circular light (Universal Light) (as shown in the following figure, with red and blue light source and polarizer (Polarization), has high recognition performance for soft plates and ceramic substrates.
5 equipped with flux dipping system (Flux Dipping Assembly), can be used for multiple suction nozzles to dip flux at the same time (as shown in the following figure).
6 the packaging methods of flip wafer include ordinary roll flip, waffle (Waffle Pack) and wafer (WaferPack). The feeder of the mounting equipment can choose belt feeder, high precision waffle disc feeder and wafer disc feeder according to the packaging of the components (as shown in the following figure).